Metal Recycling Plant Sees Major Improvement In Pump Wear Life
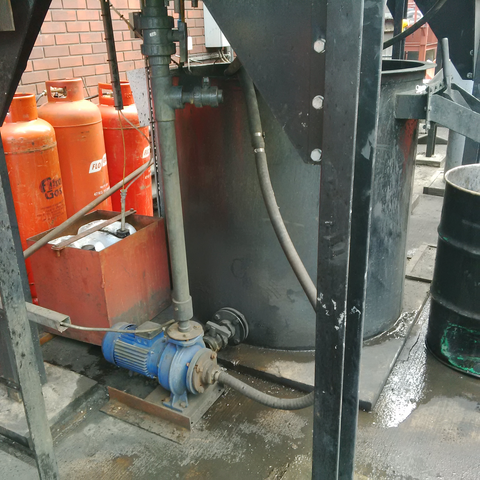
Start Date: 2014
Atlantic Pumps Representative: Daniel Hughes, Ed Smith
Client: Sims Metal Management
Address: Ulley Ln, Aston, Sheffield, S26 2DR
Phone Number: 0114 287 5272
Background
Sims Metal Management, one of the world’s leading electronics and metal recycling companies, excel in the secure and sustainable management of metals from industry, trade and the wider community. With an annual turnover exceeding £5 billion and hundreds of sites across the world, their performance and leadership on environmental, social and governance policies has seen them listed as one of the Global Top 100 Most Sustainable Corporations for the fourth year in a row.
Sims Sheffield recycling centre deals largely with general recycled metal including scrap cars, brass, bronze, iron, steel and scrap machinery. They also have their own foundry onsite to be able to finish the recycling process and deliver a complete solution.
An issue had arisen in the area of the foundry where they handle Titanium. Part of their process involved recycling dirty, used water from the dust suppression system to recover the Titanium dust but the pump they were using for this was quickly wearing out, causing downtime, high spares costs and a high time investment into keeping the system up and running. On average, the pump’s impeller was only lasting two weeks before requiring a change!
Frustrated by the high ownership costs of the pump that was installed, Sims got in touch with Atlantic Pumps to find a long term solution.

Sales Coordinator, Daniel Hughes visited the site, later commenting “We found the company had been using centrifugal water pumps designed for clean water handling and therefore not capable of pumping abrasive fluids, like those containing titanium particles. In this instance, the impellers in these pumps were lasting just two weeks!”.
Following Daniel’s visit, the Atlantic team specified a heavy duty SlurryPro pump with a rubber lined alloy which is designed for abrasive applications. Sims agreed to take the pump on a two week trial. To their delight, when the Atlantic technician opened the pump after two weeks, there were no appreciable signs of wear.
Sims went on to purchase the pump for permanent use in the application. When visiting the customer to review how the pump was operating, the customer later commented “We can’t say a bad word about the service we’ve received from Atlantic Pumps or Ed (Smith, Operations Team Leader) and they have saved us some serious money”.
Fast forward to 2017, the customer has had three years of trouble free operation, with only scheduled maintenance – compared to the fortnightly breakdowns that were occurring previously. They have also had the benefit that when they needed the spares Atlantic had them in stock for next day delivery.
For further information on any of the subjects covered in this case study, please call our team on 0800 118 2500 or email info@atlanticpumps.co.uk.